Tutorial
5 Tips to Improve Fabrication and 3D Printing from Your Rhino Design Using Grasshopper
Streamline your Rhino designs for flawless fabrication with these expert tips.
Parametric design tools like Rhino and Grasshopper offer unparalleled control over complex geometry, but ensuring that your designs translate smoothly into the physical world requires some careful preparation. Whether you're fabricating using CNC machines or preparing a model for 3D printing, here are five essential tips that will help you streamline your workflow and improve the quality of your fabrication-ready files.
1. Optimize Your Geometry for Fabrication
Fabrication processes, especially CNC and 3D printing, thrive on clean, optimized geometry. One of the first things to consider is the number of surfaces and the complexity of the forms you're creating in Rhino. Grasshopper can help by simplifying geometry with tools like the
Mesh Reduce
component. This reduces the number of polygons in a mesh without losing essential details, making the geometry more manageable for 3D printing or CNC processes.
- Grasshopper Tip: Use the
Quad Remesh
component to quickly create more fabricator-friendly mesh geometry, reducing errors during the slicing or machining process.
2. Ensure Proper Wall Thickness for 3D Printing
A common issue with 3D printing is designing parts that are either too thin or too thick, leading to structural weakness or excessive material usage. In Rhino, you can quickly measure wall thickness, but Grasshopper allows for more parametric control, where you can automate thickness adjustments across a complex model.
-
Grasshopper Tip: Use the
Offset Surface
component to ensure all surfaces are thickened appropriately for printing. This can also be paired with aBounds
component to maintain control over minimum and maximum values. -
Export Tip: Always check your model with Rhino's
Mesh Repair
tool to identify potential wall thickness issues before exporting the file for 3D printing.
3. Refine Mesh for 3D Printing
Before sending your model off for printing, the mesh must be cleaned up and optimized. When working with parametric models in Grasshopper, using components like Mesh Edges
or Weaverbird
for subdivision can significantly improve mesh quality, leading to smoother 3D prints.
-
Grasshopper Tip: Incorporate the
Weaverbird's Mesh Subdivision
tools into your pipeline to generate smooth, printable surfaces while maintaining precise control over subdivision levels. This is especially useful when printing complex organic shapes or high-resolution models. -
Export Tip: Use Rhino's
STL Export
settings wisely. Ensure that the mesh is not over-refined (i.e., overly high polygon count) or under-refined (i.e., too blocky), as this can either slow down the printer or reduce print quality.
4. Control Tolerances for CNC Fabrication
When designing for CNC fabrication, maintaining accurate tolerances between parts is crucial. This is especially true when pieces must fit together, such as in modular or interlocking designs. Grasshopper allows for precise control of parameters such as joint gaps or material shrinkage, ensuring that the final pieces come together seamlessly.
-
Grasshopper Tip: Use the
Slider
components to easily adjust tolerances between parts. This allows you to test different configurations and select the best tolerances for your fabrication method. -
Export Tip: Export your designs using Rhino's
DXF
orDWG
formats, which are commonly accepted by CNC machines. Ensure that all layers are properly assigned and that the file is formatted for 2D cutting or 3D milling based on the process you plan to use.
5. Simulate and Analyze Your Model Before Exporting
One of the advantages of using Grasshopper for parametric design is the ability to simulate and analyze the performance of your model before it's fabricated. Tools like Karamba
(for structural analysis) or Rhino's built-in curvature analysis tools can help you understand how your design will behave in real life, allowing you to make adjustments before fabrication.
-
Grasshopper Tip: Incorporate structural and material analysis components into your Grasshopper script to test the stability and durability of your design, ensuring it holds up under real-world conditions.
-
Export Tip: Always run your model through Rhino's
Prepare for 3D Printing
tool to catch any common issues such as non-manifold edges or holes in the geometry, which could cause print or fabrication errors.
Final Thoughts
Maximizing productivity in fabrication and 3D printing from your Rhino design is all about optimizing your process and ensuring that every step, from geometry to export, is finely tuned. By integrating parametric control in Grasshopper and taking advantage of Rhinoâs powerful export tools, youâll ensure that your designs are not only aesthetically pleasing but also practical and efficient to fabricate.
With these tips, you can streamline your workflow and create designs that translate smoothly into the physical world, saving time, reducing errors, and ultimately achieving better results.
Dive into the world of Grasshopper plugins today and see how they can revolutionize your approach to design and fabrication..Learn More
Posted by
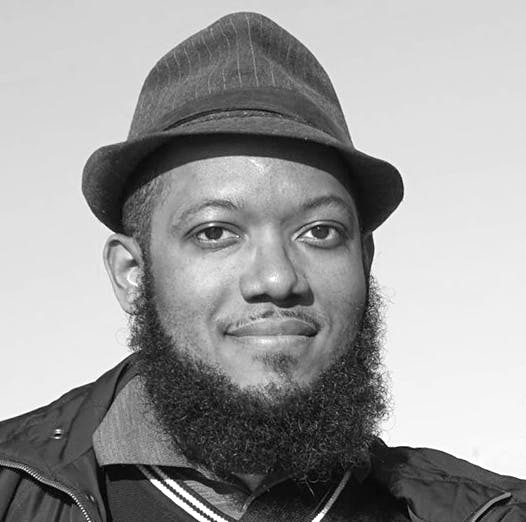
Brandon Gibbs
Senior Advocate
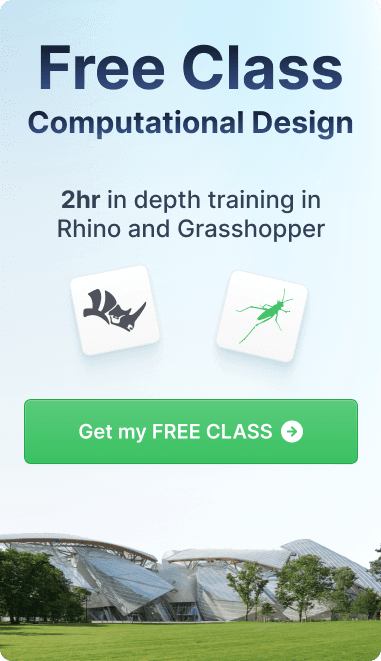
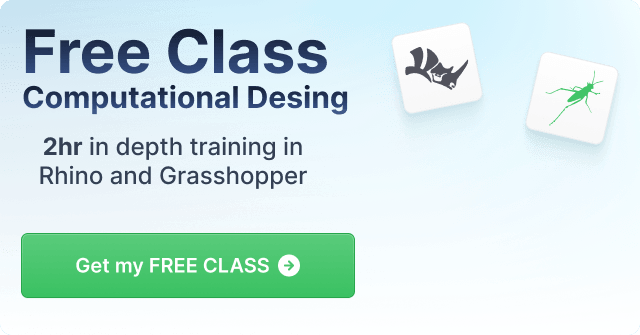